When the stress on the
stainless steel bearing workpiece is greater than the fracture limit stress of the material, the inner side or surface will be fractured and partially fractured. This phenomenon of discontinuity or fracture of the material is called crack.
There are tiny hair-like cracks on or under the surface of a material called hairlines. When the hairline expands to a corresponding extent, the phenomenon that part of the material is completely separated from the workpiece matrix is called fracture.
The cracks of stainless steel bearings are generally linear, with indeterminate directions, corresponding lengths and widths, and sharp roots and edges. Cracks can be divided into inner cracks and surface cracks, and there are also two forms of visible and invisible. For invisible cracks, non-destructive testing methods are required to be observed. Hair lines are generally thin lines, and the direction is intermittently distributed along the rolling direction of the steel, with corresponding lengths and widths, sometimes single or several.
The causes of cracks are complex, and there are many influencing factors, such as raw materials, forging, stamping and folding, heat treatment, grinding, and excessive local stress. The reason for the formation of hairline is that the bubbles or inclusions generated in the steel smelting process exist on the surface of the material after rolling deformation. Cracks that are not visible to the naked eye need to be observed by non-destructive testing.
The main measures to avoid cracks are to control the defects of raw materials in manufacturing, such as non-metallic inclusions, surface slag inclusions, folding, microscopic pores, shrinkage holes, air bubbles, etc. Control processing stress such as internal stress (thermal stress and tissue stress), grinding stress, stamping stress, etc. generated during heat treatment and quenching. In terms of use, pay attention to abnormal knocks during the installation of stainless steel bearings and excessive local stress caused by poor installation. In addition, it is necessary to ensure lubrication, enhance the sealing effect, control the inflow of external impurities, and avoid contact with corrosive substances.
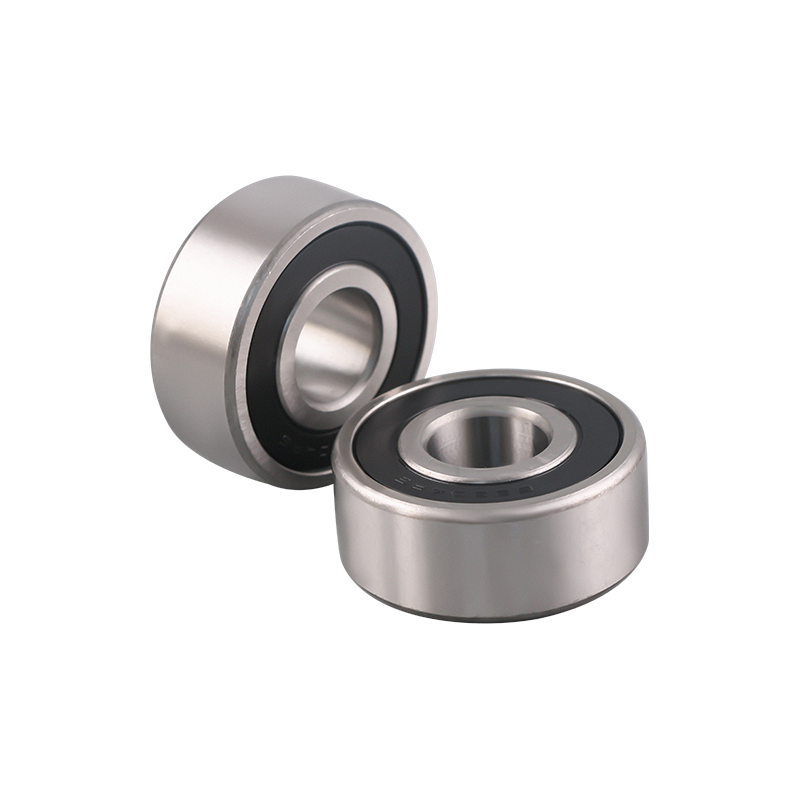