Miniature ball bearings are marvels of engineering, serving as essential components in a wide range of industries and applications. These small yet powerful devices provide smooth and precise motion control in spaces where conventional bearings cannot operate effectively. Designed to withstand high speeds, heavy loads, and limited mounting space, miniature ball bearings are a testament to precision engineering.
Miniature ball bearings are specialized rolling element bearings, consisting of an inner ring, an outer ring, a set of balls, and a cage to separate the balls. What sets them apart is their small size, with bore diameters typically ranging from a few millimeters down to just a fraction of a millimeter. These bearings are manufactured with utmost precision to ensure low friction, high durability, and efficient performance.
Miniature ball bearings can be classified into various types based on their construction and design. Some common types include deep groove ball bearings, angular contact ball bearings, thrust ball bearings, and flanged ball bearings. Each type is tailored to meet specific application requirements, such as axial or radial loads, high-speed rotation, or a combination of both.
The primary function of miniature ball bearings is to facilitate smooth and controlled motion in machinery and equipment. By utilizing rolling elements (balls) between the inner and outer rings, they minimize friction, thereby reducing energy losses and ensuring efficient operation. This characteristic makes them ideal for high-speed applications where friction would otherwise impede performance.
Despite their small size, miniature ball bearings possess impressive load-bearing capabilities. They are engineered to withstand both radial and axial loads, making them indispensable in various industries. From robotics and medical devices to aerospace and automotive applications, miniature ball bearings provide reliable support for heavy loads in compact spaces.
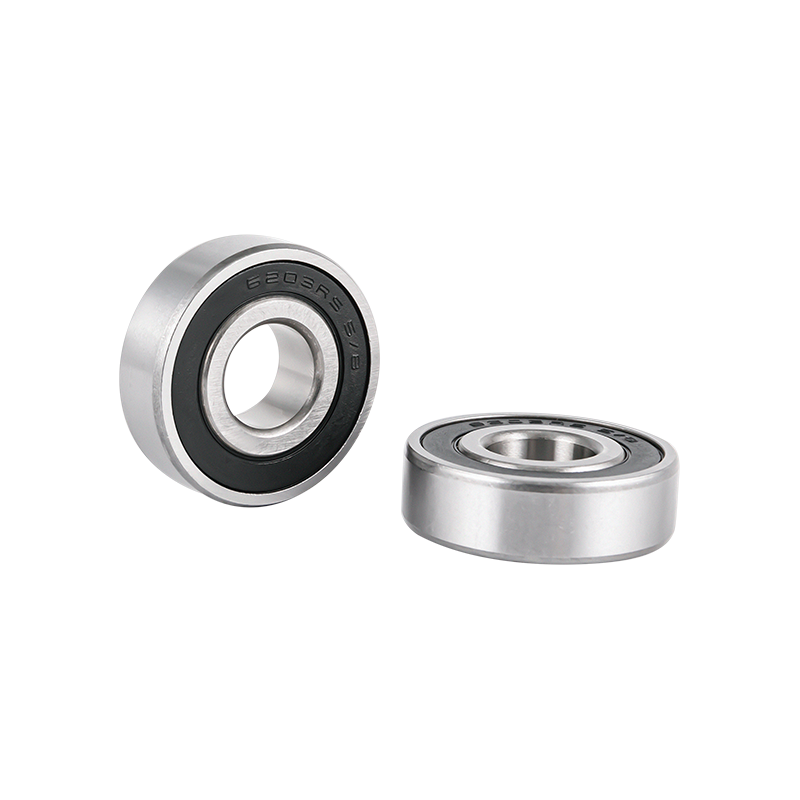