Deep groove ball thin-wall bearing is a very common type of bearing in rolling bearings. It is basically composed of an outer ring, an inner ring, a set of steel balls and a set of cages. There are two types of single-row and double-row. Deep groove ball thin-walled bearings are characterized by low frictional resistance and high rotational speed. They can be used on parts that bear radial load or combined radial and axial loads at the same time, and can also be used on parts that bear axial load. . So how to improve the performance of deep groove ball thin-walled bearings? The following editor from Prius will give you a detailed introduction.
1. Measures to improve the performance of deep groove ball thin-walled bearings
1. Sealing and dustproof
Standard industrial seals are usually made of nitrile rubber. We can also provide customized seals such as silicone rubber and Vi material for deep groove ball thin-wall bearings to meet high temperature and other extreme conditions that may be encountered.
2. Coating
For super strong anti-corrosion requirements, we can provide very thin and dense chrome plating to give deep groove ball thin-wall bearings stronger anti-corrosion ability. Unlike many conventional chrome platings, the coating does not orange peel or flake under pressure, so it retains corrosion resistance and minimizes wear. The performance of the coating has been proven in key military, aerospace and deep space applications.
3. Lubrication
Deep groove ball thin wall bearings provide a full range of lubricants to enable you to improve bearing performance in applications with special requirements such as moisture resistance, high temperature, low temperature, vacuum and low torque.
4. Internal coordination
Deep groove ball thin-wall bearings can meet the desired running performance requirements by improving the internal fit. Bearings with preload are used for high stiffness applications and bearings with radial clearance are used for low friction torque applications. In addition, standard crossed roller bearings typically have no protection against corrosion, custom seals for extreme environments, special application greases and high temperature capability.
5. Parameter design
In the design, not only the maximum rated dynamic load should be considered, but also for the small cross-section of thin-walled bearings, the value of each structural parameter should be carefully selected to improve the contact stress distribution of the bearing parts and achieve a favorable lubricating oil film formation. Good contact state, improve bearing performance and service life.
Second, the performance requirements of deep groove ball thin-walled bearings
1. High resistance to plastic deformation,
2. High anti-friction and wear performance,
3. High rotation accuracy and dimensional accuracy,
4. Good dimensional stability,
5. Long service life and high reliability.
6. For bearings that work under special conditions, there are also special requirements, such as high temperature resistance, low temperature resistance, corrosion resistance and antimagnetic properties.
3. Factors affecting the performance of deep groove ball thin-walled bearings
1. Bearing material
Bearing material is an important factor affecting the performance of deep groove ball thin-walled bearings. The rings and rolling elements of the bearing generally use high-carbon chromium bearing steel. The difference between different quality steel materials is mainly the content of oxygen and titanium, followed by the content of phosphorus and sulfur. These non-metallic elements in the steel form non-metallic inclusions that promote crack initiation when the bearing is subjected to high loads. The effect of oxygen content is large and has been shown to correlate with rolling contact fatigue life. Because oxygen atoms mostly exist in the form of oxides in metals, the particles of inclusions are large when the oxygen content is high, and the rolling contact fatigue life is related to the inclusions, so controlling the oxygen content is an effective measure to prolong the fatigue life.
2. Clearance
The radial clearance of deep groove ball thin-walled bearings is divided into original clearance, residual clearance and working clearance. The original clearance is the clearance in the free state of the bearing before installation; the residual clearance is the clearance when the bearing is inserted into the shaft or bearing seat by interference; the residual clearance is caused by the dimensional deformation caused by the internal temperature difference of the bearing and the load. The bearing is elastically deformed and increased or decreased. At this time, the clearance is the working clearance. The radial clearance of the rolling bearing directly affects the load distribution inside the bearing, thereby affecting the vibration characteristics and fatigue life of the bearing. Excessive clearance will reduce the bearing area inside the bearing, cause elastic deformation of the rolling element and the ferrule, increase the stress on the contact surface, shorten the bearing life and reduce the bearing rotation accuracy, and generate radial circular runout, thereby causing vibration and vibration. Noise; if the clearance is too small, it is easy to increase the friction and heat, and the temperature rise will increase, which will make the effective clearance smaller or the interference larger, causing the bearing to lock.
3. Grease
Greases consist of base oils, thickeners and additives. The anti-fatigue wear ability of deep groove ball thin-walled bearings is related to the viscosity of lubricating oil. Under certain conditions, it increases with the increase of lubricating oil viscosity. The adverse effect of the amount of grease filling on the bearing performance is: too much grease is filled, and the bearing generates a lot of thermal energy during operation and is prone to leakage, but at this time, the failure of the bearing is mainly due to the weak link of the material itself under the contact surface, such as inclusions or Uneven organization, etc.; too little grease, there is no thick enough oil film at the rolling contact position inside the bearing to isolate the rolling element and the ferrule, and there will be direct contact between the materials to varying degrees, resulting in mixed friction, causing material surface wear and reducing fatigue. life.
4. Dust cover and sealing ring
Deep groove ball thin-walled bearings are mixed with wear particles, foreign matter or moisture, etc., which will affect the lubricating performance and film-forming properties of the grease, and further aggravate the bearing failure. Therefore, it is necessary to choose a dust cover or a sealing ring to ensure effective lubrication and reduce Vibration and noise reduction performance. The dust cover type is mainly used to prevent the entry of external dust, and the waterproof performance is average; the contact type rubber sealing ring type can prevent the entry of external pollution while preventing the internal grease, and the dustproof performance is better than that of the dust cover. Ring contact, the friction torque generated during operation is large, there is a limit to the limit use speed, and the applicable temperature range is relatively small.
5. Processing technology
The common bearing processing process is mainly composed of inner and outer ring processing, inner and outer ring assembly, cleaning and inspection, grease filling and packaging. For the inner and outer rings of deep groove ball bearings, the main technical indicators that affect the vibration are the inner and outer groove waviness and surface roughness, followed by roundness and surface bumps. For the rolling elements of deep groove ball bearings, the main technical indicators affecting vibration are waviness, roughness and circular deviation. The vibration and noise performance can be improved by increasing the number of rough grinding, controlling the roundness and waviness of the inner and outer grooves, and increasing the number of super-finishing inner and outer grooves to ensure the roughness requirements in the process flow.
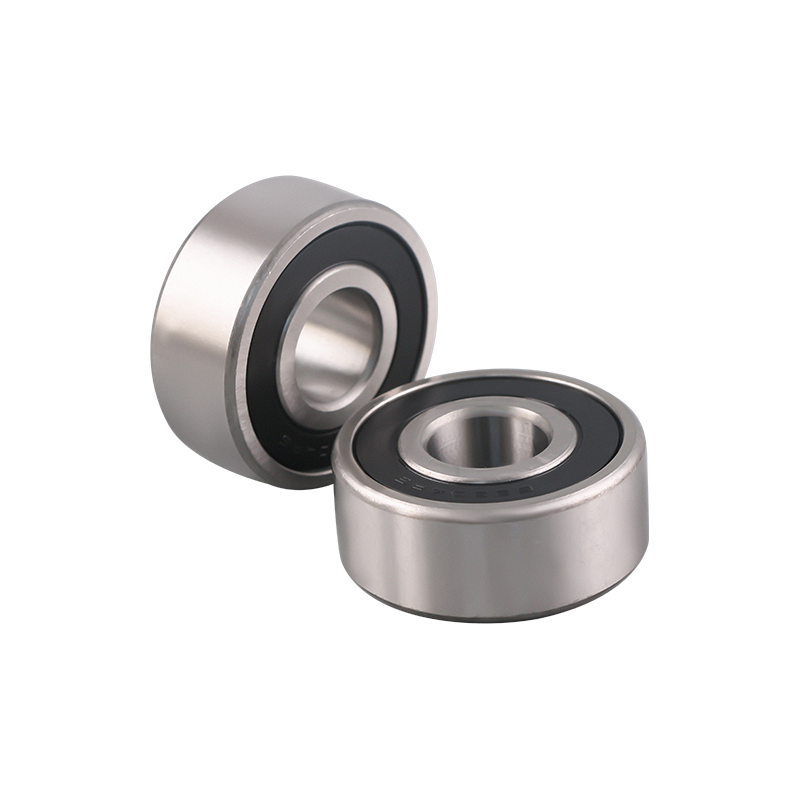